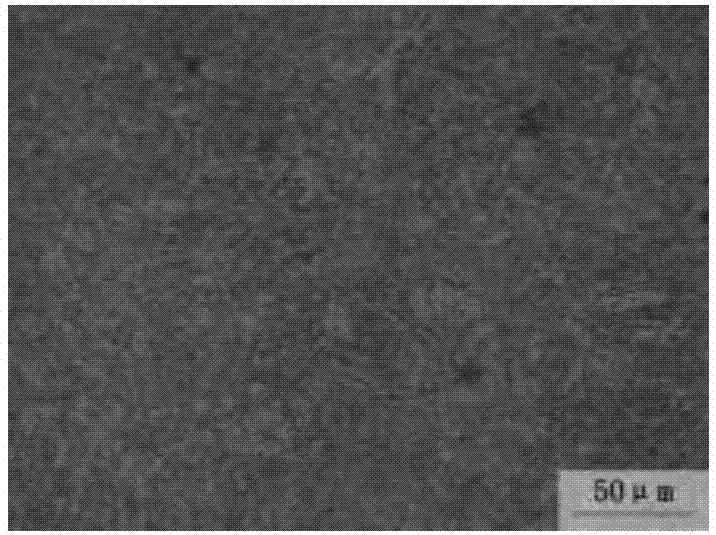
本發(fā)明涉及一種預埋槽,具體說,涉及一種耐腐蝕槽道及其生產(chǎn)方法。
背景技術:
:在軌道交通、地下管廊和幕墻中,有很多產(chǎn)品或設備需要固定在墻上或天花板上。傳統(tǒng)的方法多采用膨脹螺栓、預埋鋼板、化學錨栓等方式固定,但存在難以克服的破壞墻體結構、施工復雜、維護困難等固有缺點,已不適應越來越苛刻的使用條件。預埋槽通常用槽道為主要原材料,但是,現(xiàn)在槽道并不能適應這種高濕度環(huán)境,往往容易出現(xiàn)腐蝕現(xiàn)象,影響了使用壽命。技術實現(xiàn)要素:本發(fā)明所解決的技術問題是提供一種耐腐蝕槽道,具有優(yōu)異的耐腐蝕性能。技術方案如下:一種耐腐蝕槽道,其化學成分的質量百分比包括c0.08~0.12%、si0.20~0.35%、mn0.85~1.05%、p≤0.020%、s≤0.008%、cr0.90~1.10%、ni0.30~0.40%、cu0.20~0.50%、re0.0035~0.02%、als0.01~0.03。進一步:re選用la或者ce。進一步:re選用la和ce的混合稀土。進一步:其有害元素要求的質量百分比包括as≤0.015%、sn≤0.015%、pb≤0.010%、sb≤0.010%、bi≤0.010%。進一步:c0.10~0.12%,si0.25~0.27%,mn0.95~1.02%,p0.008~0.011%,s0.005~0.007%,cr0.94~0.98%,ni0.30~0.32%,cu0.25~0.28%、re0.0035~0.0060%,als0.018~0.022%。本發(fā)明所解決的另一個技術問題是提供一種耐腐蝕槽道的生產(chǎn)方法,得到的耐腐蝕槽道具有優(yōu)異的耐腐蝕性能。技術方案如下:一種耐腐蝕槽道的生產(chǎn)方法,包括:根據(jù)成分設計進行冶煉;冶煉過程包括鐵水預處理、頂?shù)讖痛缔D爐冶煉、lf爐外精煉、vd真空處理、方坯連鑄機澆注;軋制過程包括坯料的加熱和坯料的軋制,坯料的加熱溫度為1100℃-1150℃;坯料的軋制包括粗軋機軋制和精軋機組連續(xù)軋制成型,軋制成的槽道的化學成分按照質量百分比包括c0.08~0.12%、si0.20~0.35%、mn0.85~1.05%、p≤0.020%、s≤0.008%、cr0.90~1.10%、ni0.30~0.40%、cu0.20~0.50%、re0.0035~0.02%、als0.01~0.03。進一步:頂?shù)讖痛缔D爐冶煉采用單渣操作,終渣堿度控制在3.0;氧槍為五孔拉瓦爾噴頭,采用低、高、低槍位控制;采用硅錳、cu、ni合金化,鋁錳鐵合金進行終脫氧,轉爐出鋼后加中碳鉻鐵;轉爐終點的質量百分比成分為c0.06%,mn0.14%,p0.008%,s0.027%;轉爐終點的溫度為1637℃;lf爐外精煉對鋼水進行升溫、成分微調和脫s操作,在全程吹氬狀態(tài)下精煉,加入造渣材料、錳鐵、鋁線進行脫氧合金化;鋼水精煉就位溫度為1552℃,離位溫度1669℃,采用有鋁脫氧、脫硫和成分微調,并在精煉后期加入鎳鐵及補加鉻鐵,精煉就位成分質量百分比中,c為0.09%,si為0.19,mn為0.84,p為0.011,s為0.007,als為0.01,cr為0.88,ni為0.31,cu為0.29,as為0.001;精煉離位成分質量百分比中,c為0.11%,si為0.23,mn為0.98,p為0.015,s為0.005,als為0.03,cr為0.99,ni為0.34,cu為0.29,as為0.001;vd抽真空處理中,深真空時間13min,真空處理時間26min,vd前溫度1670℃,vd后溫度1620℃;vd處理后喂硅鈣線和稀土絲,對鋼水中夾雜物進行變性處理,并進行軟吹氬,軟吹時間14分鐘;連鑄后得到坯料,澆鑄的過熱度為25℃,拉速為0.6m/min。進一步:坯料的加熱過程中,坯料用鋸床鋸切成成所需尺寸,由軋鋼車間吊車將坯料成組吊到上料臺架上,由翻轉設備將坯料翻轉到鏈條輸送設備上,坯料經(jīng)輸送到中頻感應加熱爐內進行加熱,當坯料加熱到1100℃-1150℃時,加送輥道再送入一根冷坯料,同時加熱好的坯料出爐,沿滑道下滑至坯料輸送輥道;加熱好的坯料通過輸送輥道首先送入粗軋機軋制,在這個過程中坯料被壓薄、切深、延長、變形,粗軋后再進入軋機組軋制2個道次,坯料繼續(xù)被延伸成型,此時屬預成型階段,最后進入精軋機組進行連續(xù)軋制,制成槽道。進一步:軋制過程還包括矯直機矯直及檢驗和鋸切;矯直機矯直及檢驗過程中,坯料送到冷床上的槽道冷卻后,通過冷床輸出輥道送入十四輥矯直機進行矯直,產(chǎn)品符合要求后進入下一道工序;矯直后的槽道進行彎曲度、平直度的檢驗,不合格品再次進入矯直程序。進一步:re選用la或者ce,槽道有害元素要求的質量百分比包括as≤0.015%、sn≤0.015%、pb≤0.010%、sb≤0.010%、bi≤0.010%。與現(xiàn)有技術相比,本發(fā)明技術效果包括:本發(fā)明中槽道改善了夾雜物形態(tài),提高了鋼的潔凈度,從而提高了抗腐蝕性能。并且,使用槽道的耐腐蝕預埋槽的使用工藝獨特,能夠加快施工進度,并且使用壽命長。附圖說明圖1是本發(fā)明中槽道珠光體的金相圖;圖2是本發(fā)明中槽道鐵素體的金相圖。具體實施方式下面參考示例實施方式對本發(fā)明技術方案作詳細說明。然而,示例實施方式能夠以多種形式實施,且不應被理解為限于在此闡述的實施方式;相反,提供這些實施方式使得本發(fā)明更全面和完整,并將示例實施方式的構思全面地傳達給本領域的技術人員。1、本發(fā)明的鋼種成分設計原則。成分設計主要從各項性能和提高抗大氣腐蝕能力兩方面考慮。由于軋成預埋槽道后不需要進行軋后熱處理,因此塑性和韌性完全可以滿足用戶要求,而最關鍵的是強度和抗大氣腐蝕性能.通過控制c和mn含量滿足強度要求,加入合金提高鋼的淬透性和耐腐蝕能力,圍繞如何提高抗腐蝕性能來選擇合金元素和軋制工藝,通過分析各合金元素對腐蝕影響因素確定所需加入的合金元素。2、本發(fā)明的鋼種設計思路。根據(jù)各元素在鋼中的主要作用,選c和mn作為主要強化元素,以保證屈服和抗拉強度;選cr和ni、cu作為主要抗腐蝕元素,控制s和p等有害元素的含量,同時加入re改善夾雜物形態(tài),提高鋼的潔凈度,從而提高鋼的抗腐蝕性能。3、槽道的化學成分的作用。(1)化學元素對硫化氫應力腐蝕的影響。碳:c是最有效的強化元素,對抗h2s影響不大,碳的含量主要從考慮鋼的強度和韌性的需求來確定。硅:si具有阻礙碳化物析出的趨向,是非碳化物形成元素。硅還能提高鋼的屈服強度,降低碳在奧氏體中的溶解度,促使碳化物沿晶界析出,降低鋼的韌性。同時硅元素含量偏高時,易偏析于晶粒邊界,在應力腐蝕時會助長晶間裂紋的形成。錳:鋼中含有一定量的mn可減弱應力腐蝕環(huán)境下s的有害作用,然而考慮到過高的錳含量會使裂紋敏感率及裂紋長度敏感率急劇升高,材料對hic的敏感性增大。mn促進有害元素p、s、sn、sb等向晶界偏析,偏析在晶界的p、sn、sb等和h能發(fā)生交互作用,從而使晶界鍵合力大幅度下降,容易引起氫致沿晶斷裂。因此,控制鋼中mn的含量對提高鋼材的抗腐蝕性能有重要意義。但是,除c以外,mn和si是提高強度的最有效且最便宜的合金元素??紤]到mn對大氣腐蝕的有害程度比si要小,故選mn作為提高強度的合金元素。鉻:cr含量對鋼的抗腐蝕性能的影響很大,能促使鋼的表面形成致密的氧化膜,提高鋼的鈍化能力。鋼中cr含量愈多,硫對鋼的相對腐蝕就愈小。cr能增進鋼的硬化和滲碳作用,使鋼在高溫時仍具高強度,同時能增加鋼的耐磨耗性,提高鋼的淬火溫度,能增進鋼的抗腐蝕性。cr在結構鋼和工具鋼中,能顯著提高強度、硬度和耐磨性,但同時降低塑性和韌性。又能提高鋼的抗氧化性和耐腐蝕性,因而是不銹鋼,耐熱鋼的重要合金元素。鎳:在耐腐蝕鋼種,ni的存在可抑制cu的熱脆性,ni含量每提高0.1%,可使腐蝕引起的損失降低4%,腐蝕速率降低7%,侵入250μm深度所需的時間提高12%。同時能提高鋼的強度和韌性,提高淬透性。含量高時,可顯著改變鋼和合金的一些物理性能,提高鋼的抗腐蝕能力。鎳能提高鋼的強度,而又保持良好的塑性和韌性。鎳對酸堿有較高的耐腐蝕能力,在高溫下有防銹和耐熱能力。鎳在鋼中的影響有:a.增進鋼的硬化能力。b.能降低熱處理時的淬火溫度,因而在熱處理時變形小。c.能增加鋼的韌性。d.高鎳合金鋼能耐腐蝕,例如:不銹鋼就含有8%左右的鎳。硫:硫是耐腐蝕鋼中的有害元素。磷:固溶強化及冷作硬化作用很好,與銅聯(lián)合使用,提高低合金高強度鋼的耐大氣腐蝕性能,但降低其冷沖壓性能,與硫、錳聯(lián)合使用,改善切削性,增加回火脆性及冷脆敏感性;在鋼的凝固過程中,由于受碳對凝固前沿溶質擴散行為的影響,p偏析會顯著增加,尤其在鑄坯凝固末端會產(chǎn)生磷的富集,成為氫的聚集源。在一般情況下,磷是鋼中有害元素,增加鋼的冷脆性,使焊接性能變壞,降低塑性,使冷彎性能變壞。因此通常要求鋼中含磷量小于0.045%,優(yōu)質鋼要求更低些。銅:它的突出作用是改善普通低合金鋼的抗大氣腐蝕性能,特別是和磷配合使用時更為明顯;銅能提高強度和韌性,特別是大氣腐蝕性能。缺點是在熱加工時容易產(chǎn)生熱脆,銅含量超過0.5%塑性顯著降低。當銅含量小于0.50%對焊接性無影響;合金鋼中銅之含量不可以超過1.5%,否則會使鋼變脆,此外銅在鋼中有抵抗大氣腐蝕之性能。低碳鋼內含銅1%,其抵抗大氣腐蝕性約較不含銅者高出四倍。在不銹鋼中加銅3~4%,亦有助不銹鋼之防蝕作用。含量低時,作用和鎳相似,含量較高時,對熱變形加工不利,如超過0.30%時,在熱變形加工時導致高溫銅脆現(xiàn)象,含量高于0.75%時,經(jīng)固溶處理和時效后可產(chǎn)生時效強化作用。在低碳合金鋼中,特別是與磷同時存在,可提高鋼的抗大氣腐蝕性,2%~3%的銅在不銹鋼中可提高對硫酸、磷酸及鹽酸等的抗腐蝕性及對應力腐蝕的穩(wěn)定性。(2)稀土對鋼抗腐蝕性的影響。在鋼中加入適當?shù)南⊥?,有利于脫氧、脫硫、除去氣體,減少有害元素的影響,顯著提高鋼的韌性、耐磨性、抗蝕性、改善鋼的焊接性能和低溫性能。具體來說稀土在鋼中的作用主要有以下幾個方面:1)凈化鋼液稀土金屬的化學性質異?;钴S,在鋼液溫度(1550~1600℃)下,同氧、硫、氮、碳和氫等有害雜質的作用能力極強,分別作用生成密度小、熔點高的化合物而浮于鋼液表面可以被分離出去,因而起到凈化鋼液的作用。稀土金屬是煉鋼工業(yè)中良好的脫氧劑和脫硫劑。2)變質作用鋼鐵等金屬的斷裂過程是裂縫不斷發(fā)生和發(fā)展的過程,夾雜物往往作為顯微裂縫的發(fā)源地,因而對于與斷裂過程密切相關的一系列性能,如塑性、韌性以及疲勞性能會帶來顯著的影響。稀土在鋼中的凈化變質作用,正是改變了鋼中夾雜物的數(shù)量、性質、形態(tài)、大小和分布,從而顯著提高鋼材的機械性能。一般鋼中,其夾雜主要是硅、鐵、錳、鋁的氧化物、硫化物、硫氧化物,其中大部分在鋼液凝固之前上浮成渣。對鋼性能危害較大的夾雜物是硫化錳,硫以細長的mns形式存在。在軋鋼時,夾雜物mns(沿鋼的晶界分布)沿軋制方向延伸,可塑性大,強度低,因而顯著的降低了鋼的韌性和鋼的橫向性能。導致管道、鋼材等在寒冷地區(qū)發(fā)生延展性破壞和氫致裂紋。經(jīng)稀土處理的鋼,由于鋼液得到凈化,其中有害的硫化錳大為減少。那些尚未除盡的硫化物,即鋼中長條狀mns被球狀、紡錘狀稀土硫化物和硫氧化物所取代,并使夾雜物細化和彌散分布,從而顯著提高了鋼的橫向沖壓性能,并改善了鋼材的各向異性。此外,經(jīng)稀土處理,稀土可使鋼中脆性氧化鋁夾雜轉變成球狀稀土鋁酸鹽(realo3)等,顯著提高鋼的抗疲勞性能。3)細化晶粒稀土化合物微小的固態(tài)質點提供了異質形核或在結晶界面上的偏聚,阻礙晶胞長大。在鋼受熱時,奧氏體的晶粒會長大變粗,但經(jīng)過稀土處理的鋼其晶粒較細,這是由于稀土金屬形成高熔點穩(wěn)定的化合物成為極微小的異質晶核,提供了細化結晶的良好條件,因此經(jīng)稀土處理的鋼具有細化晶粒的效果。此外,鑭、鈰等稀土金屬可阻止無鎳的鉻錳鋼在1100~1250℃溫度范圍奧氏體晶粒的長大,由于這些結晶和晶界情況的改善,一些鋼種加入稀土后在鋼材表面形成致密的稀土氧化膜,提高了耐熱、抗腐蝕和抗氧化性能,對高溫持久強度和抗蠕變性能也有所改善。4)微合金化鋼的潔凈度不斷提高,稀土元素的微合金強韌化作用日益突出。微合金化的強韌化程度決定于微量稀土元素的固溶強化、稀土元素與其它溶質元素的交互作用、稀土的存在狀態(tài)(原子、夾雜物或化合物),特別是在晶界的偏聚,以及稀土對鋼表面和基體組織結構的影響等。由稀土—鐵系相圖可知,稀土元素在鐵液中與鐵原子是互溶的,但其在鐵基固溶體中的分配系數(shù)極小,在鐵液凝固過程中,被固/液界面推移最后富集于枝晶間或晶界。由于稀土原子半徑比鐵原子大,對固溶體能提供強化作用。固溶在鋼中的稀土往往通過擴散機制富集于晶界,減少了雜質元素在晶界的偏聚。未加稀土的鋼,雖然硫含量很低,但硫磷仍明顯偏聚在晶界,磷比硫在晶界偏聚更為嚴重。加稀土后,由于稀土在晶界的偏聚,明顯改善了硫和磷在晶界的偏聚,并隨著稀土固溶量的增加,偏聚逐漸減小。晶界上硫的偏聚要比磷偏聚更容易消除。5)抗氫脆致應力腐蝕稀土金屬有很強的吸氫作用并形成相應的稀土氫化物,從而抑制鋼中氫引起的氫脆。20世紀80年代,一些研究發(fā)現(xiàn)添加稀土能減少和消除鋼的氫致裂紋(hic)。實驗表明,鋼中鈰或鑭的含量要超過0.1%時才可產(chǎn)生明顯效果,這時可能在re-fe共晶體內形成了氫化物。隨著海洋、石油和化學工業(yè)的發(fā)展,鋼中加入稀土以提高抗氫致裂紋將是今后稀土在鋼中應用最具潛力的新領域。槽道的生產(chǎn)方法,總的工藝流程包括:轉爐冶煉→軋制。具體步驟如下:步驟1:轉爐冶煉;鐵水預處理→頂?shù)讖痛缔D爐冶煉→lf爐外精煉→vd真空處理→方坯連鑄機澆注。1、頂?shù)讖痛缔D爐冶煉。煉鋼采用頂?shù)讖痛缔D爐冶煉,單渣操作,終渣堿度控制在3.0,保證脫磷效果;氧槍為五孔拉瓦爾噴頭,采用低—高—低槍位控制;采用硅錳、cu、ni合金化,鋁錳鐵合金進行終脫氧,轉爐出鋼后加中碳鉻鐵。轉爐終點控制成分和溫度,具體參數(shù)見表1。表1轉爐終點成分和溫度(質量百分比%)c/%mn/%p/%s/%溫度/℃0.060.140.0080.02716372、lf爐外精煉。鋼水罐運至lf鋼包爐精煉,對鋼水進行升溫、成分微調和脫s操作。在全程吹氬狀態(tài)下精煉,加入白灰、礬土、螢石、電石等造渣材料;加入錳鐵、鋁線進行脫氧合金化,lf爐白渣精煉實現(xiàn)深度脫硫。鋼水精煉就位溫度為1552℃,離位溫度1669℃。在精煉爐采用有鋁脫氧、脫硫和成分微調,并在精煉后期加入鎳鐵及補加鉻鐵。精煉就位、離位成分見表2。表2lf爐鋼水就位、離位成分(質量百分比%)csimnpsalscrnicuas就位0.090.190.840.0110.0070.10.880.310.290.001離位0.110.230.980.0150.0050.30.990.340.290.0013、vd真空處理。精煉后采用vd抽真空處理,vd處理時間及溫度、真空度見表3。vd處理后喂硅鈣線200m,稀土絲200m,對鋼水中夾雜物進行變性處理,并進行軟吹氬,軟吹時間14分鐘。表3vd處理時間深真空時間/min真空處理時間/minvd前溫度/℃vd后溫度/℃1326167016204、連鑄后得到坯料。vd后的鋼水罐轉送到圓坯連鑄機進行澆鑄,鑄坯規(guī)格為319×410㎜,澆鑄工藝參數(shù)見表4。表4連鑄工序參數(shù)過熱度△t/℃拉速v/m/min250.65、鑄坯的質量檢驗。連鑄坯具有良好的低倍組織是保證預埋槽道合格率的首要條件。由于在煉鋼連鑄生產(chǎn)中嚴格控制了過熱度與拉速的匹配,選擇了合適的二冷配水工藝和保護渣,因此鑄坯表面和內部質量控制較好,鑄坯缺陷級別為0-1級,連鑄坯組織較為致密,無肉眼可見的殘余縮孔、白點、裂紋、氣泡、金屬異物、夾雜等。硫印結果較好,達到相關標準的要求。表5硫印檢驗結果/級中間裂紋中心裂紋皮下裂紋夾雜物0101表6各項性能檢驗結果表7金相檢驗結果步驟2:軋制;步驟21:坯料的加熱;坯料首先用鋸床鋸切成成所需尺寸,由軋鋼車間吊車將坯料成組吊到上料臺架上,又由翻轉設備將坯料翻轉到鏈條輸送設備上輸送到中頻感應加熱爐內進行加熱。當坯料加熱到1100℃-1150℃時,加送輥道再送入一根冷坯料,同時加熱好的坯料出爐,沿滑道下滑至坯料輸送輥道。步驟22:坯料的軋制;加熱好的坯料通過輸送輥道首先送入粗軋機軋制,在這個過程中坯料被壓薄、切深、延長、變形,粗軋后再進入軋機組軋制2個道次,坯料繼續(xù)被延伸成型,此時屬預成型階段,最后進入連軋機組進行連續(xù)軋制成型,確保軋件得到所需的規(guī)格尺寸及壁厚,以及精確鉚鉤的成型,即軋制成所需槽道。槽道的化學成分如表8所示。表8化學成分要求/質量百分比%本優(yōu)選實施例中,re選用的la或者ce,也可以選用la、ce混合稀土。表9有害元素要求/質量百分比%assnpbsbbi≤0.015≤0.015≤0.010≤0.010≤0.010槽道的成分檢驗。分批次取樣后,用化學分析法對成分進行了檢驗,檢驗結果見下表10。表10槽道的成分/質量百分比%2017年1月18日,槽道經(jīng)中國鐵道科學研究院金屬及化學研究所檢驗,得出檢驗報告((2017)jhc字第307號),具體參數(shù)見表11。表11通過對比可以看出,槽道的耐腐蝕的各項指標均明顯高于q345b鋼材。步驟23:矯直機矯直及檢驗;送到冷床上的槽道冷卻后,通過冷床輸出輥道送入十四輥矯直機進行矯直,產(chǎn)品符合要求后進入下一道工序。步驟24:鋸切;矯直后的槽道由人工進行彎曲度、平直度的檢驗,不合格品再次進入矯直程序。通過卡尺精確測量壁厚,根據(jù)客戶的需要進行鋸切。步驟3:包裝。將檢測完畢合格的槽道進行槽道內腔加填充物(低密度聚乙烯),槽道兩端加上端蓋,槽道槽口表面覆蓋單面膠等進行包裝。分批次取樣后,用化學分析法對成分進行了檢驗,檢驗結果見下表10。如圖1所示,是本發(fā)明中槽道珠光體的金相圖;如圖2所示,是本發(fā)明中槽道鐵素體的金相圖。軋態(tài)的組織為珠光體和鐵素體。晶粒度8.5級。金相檢驗結果見表12。表12金相檢驗結果槽道在沖孔和鉚接預埋桿后形成耐腐蝕預埋槽,耐腐蝕預埋槽的使用方法如下:1、澆鑄混凝土時,將耐腐蝕預埋槽放入混凝土預埋,槽口留在混凝土表面;2、待混凝土凝固后,現(xiàn)場組裝時,將t形螺栓端頭放入槽道內腔,并軸向轉軸t形螺栓90°,使端頭卡在槽道內腔;3、將螺母安裝在t形螺栓上并擰緊,使得t形螺栓完全固定在耐腐蝕預埋槽上;4、將支架固定在t形螺栓上,完成現(xiàn)場組裝。本發(fā)明所用的術語是說明和示例性、而非限制性的術語。由于本發(fā)明能夠以多種形式具體實施而不脫離發(fā)明的精神或實質,所以應當理解,上述實施例不限于任何前述的細節(jié),而應在隨附權利要求所限定的精神和范圍內廣泛地解釋,因此落入權利要求或其等效范圍內的全部變化和改型都應為隨附權利要求所涵蓋。當前第1頁12