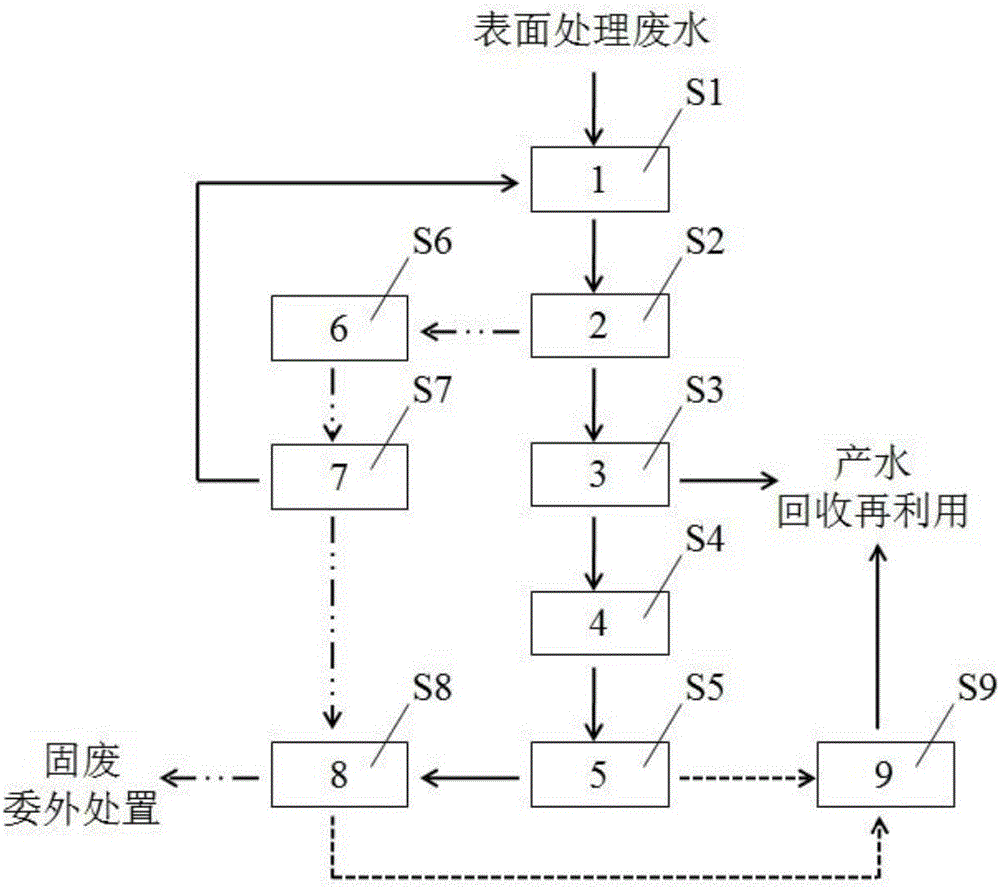
本發(fā)明屬于廢水處理
技術(shù)領(lǐng)域:
,涉及一種用于處理表面處理廢水的系統(tǒng)以及使用該系統(tǒng)對(duì)表面處理廢水進(jìn)行零排放處理的方法。
背景技術(shù):
:金屬表面處理是一種利用物理、化學(xué)或其他方法在金屬基材表面形成一層具有特殊功能的覆蓋層的工藝,其目的在于提高金屬基材的耐蝕性、耐磨性、可裝飾性等性能。在金屬表面處理過程中,脫脂、水洗、純水洗、硅烷處理四個(gè)工段會(huì)產(chǎn)生大量廢水。這些廢水中的污染物成份比較復(fù)雜,通常含有大量的堿性或酸性物質(zhì)、有機(jī)物以及一定量的金屬離子和非金屬離子,處理難度較大,直接排放到環(huán)境中會(huì)對(duì)水和土壤造成嚴(yán)重污染。目前,表面處理廢水的常用處理方法依次包括下列步驟:隔油處理、化學(xué)氧化處理、混凝沉淀處理和多級(jí)生物處理,廢水經(jīng)過生物處理后直接排放。但是,該方法存在以下問題:(1)化學(xué)氧化處理的運(yùn)營成本高昂,并且化學(xué)氧化藥劑的投加量不當(dāng)會(huì)對(duì)生物處理系統(tǒng)造成毒害作用;(2)由于廢水水質(zhì)的波動(dòng)性較大,導(dǎo)致生物處理系統(tǒng)的穩(wěn)定性較差,廢水處理的可持續(xù)性也隨之變差,并且生物處理系統(tǒng)在遭到破壞后的恢復(fù)過程難度較高且周期較長;(3)該方法對(duì)重金屬離子的去除效果較差,處理后直接排放仍有可能污染環(huán)境,不符合國家提倡的零排放政策,并且直接排放是對(duì)水資源的嚴(yán)重浪費(fèi);(4)該方法包括多級(jí)生物處理,占地面積大,不利于大規(guī)模工業(yè)化推廣。因此,在表面處理廢水處理
技術(shù)領(lǐng)域:
中,亟需開發(fā)一種既經(jīng)濟(jì)高效又簡便易行的處理方法以及與之配套的處理系統(tǒng)。技術(shù)實(shí)現(xiàn)要素:為了解決現(xiàn)有的表面處理廢水處理方法存在的成本高、穩(wěn)定性及可持續(xù)性差、水資源浪費(fèi)嚴(yán)重、設(shè)備占地面積大等問題,本發(fā)明的目的在于提供一種金屬表面處理廢水的零排放處理系統(tǒng)及使用該系統(tǒng)進(jìn)行廢水處理的方法。為了實(shí)現(xiàn)上述目的,本發(fā)明采用如下技術(shù)方案:一種表面處理廢水的處理系統(tǒng),其包括廢水收集裝置、預(yù)處理裝置、膜處理裝置、預(yù)熱裝置、膜蒸餾裝置、污泥儲(chǔ)存裝置、固液分離裝置、干化裝置和冷凝裝置;其中:所述廢水收集裝置與所述預(yù)處理裝置受控連通;所述預(yù)處理裝置還分別與所述膜處理裝置和所述污泥儲(chǔ)存裝置受控連通;所述膜處理裝置與所述預(yù)熱裝置受控連通;所述預(yù)熱裝置與所述膜蒸餾裝置受控連通;所述膜蒸餾裝置分別與所述干化裝置和所述冷凝裝置受控連通;所述污泥儲(chǔ)存裝置還與所述固液分離裝置受控連通;所述固液分離裝置分別與所述干化裝置和所述廢水收集裝置受控連通;所述干化裝置還與所述冷凝裝置受控連通。在上述表面處理廢水的處理系統(tǒng)中,所述廢水收集裝置的出口與所述預(yù)處理裝置的入口連通。在上述表面處理廢水的處理系統(tǒng)中,所述預(yù)處理裝置的至少一個(gè)出口(預(yù)處理上清液出口)與所述膜處理裝置的入口連通,所述預(yù)處理裝置的至少一個(gè)出口(污泥出口)與所述污泥儲(chǔ)存裝置的入口連通。在上述表面處理廢水的處理系統(tǒng)中,所述膜處理裝置的至少一個(gè)出口(濃水出口)與所述預(yù)熱裝置的入口連通,所述膜處理裝置的至少一個(gè)出口(產(chǎn)水出口)用于將產(chǎn)水排出,以便進(jìn)行回收再利用。在上述表面處理廢水的處理系統(tǒng)中,所述預(yù)熱裝置的出口與所述膜蒸餾裝置的入口連通。在上述表面處理廢水的處理系統(tǒng)中,所述膜蒸餾裝置的至少一個(gè)出口(膜蒸餾濃縮液出口)與所述干化裝置的至少一個(gè)入口(膜蒸餾濃縮液入口)連通,所述膜蒸餾裝置的至少一個(gè)出口(水蒸氣出口)與所述冷凝裝置的至少一個(gè)入口連通。在上述表面處理廢水的處理系統(tǒng)中,所述污泥儲(chǔ)存裝置的出口與所述固液分離裝置的入口連通。在上述表面處理廢水的處理系統(tǒng)中,所述固液分離裝置的至少一個(gè)出口(固體組分出口)與所述干化裝置的至少一個(gè)入口(固體組分入口)連通,所述固液分離裝置的至少一個(gè)出口(液體組分出口)與所述廢水收集裝置的至少一個(gè)入口連通。在上述表面處理廢水的處理系統(tǒng)中,所述干化裝置的至少一個(gè)出口(水蒸氣出口)與所述冷凝裝置的至少一個(gè)入口連通,所述干化裝置的至少一個(gè)出口(固廢出口)用于將固體廢棄物排出,以便進(jìn)行委外處置。上述表面處理廢水的處理系統(tǒng)的使用方法,其包括下列步驟:S1、廢水的收集與混合:將各路廢水收集在廢水收集裝置中并加以混合(用于保證水質(zhì)和水量的穩(wěn)定),形成混合廢水;S2、混合廢水的預(yù)處理:使S1中形成的混合廢水進(jìn)入預(yù)處理裝置中,加入破乳劑后調(diào)節(jié)pH值至8~10,加入混凝劑和絮凝劑后進(jìn)行沉淀(用于降低廢水中油類物質(zhì)及懸浮物的含量),形成污泥和預(yù)處理上清液;S3、預(yù)處理上清液的膜處理:使S2中形成的預(yù)處理上清液進(jìn)入膜處理裝置中,依次經(jīng)過精密過濾、超濾(精密過濾和超濾用于截留預(yù)處理上清液中的懸浮物,避免對(duì)反滲透膜造成污染)和反滲透(RO),形成產(chǎn)水和濃水;S4、濃水的預(yù)熱:使S3中形成的濃水進(jìn)入預(yù)熱裝置中進(jìn)行預(yù)熱(增加濃水的蒸汽壓),形成預(yù)熱濃水;S5、預(yù)熱濃水的膜蒸餾:使S4中形成的預(yù)熱濃水進(jìn)入膜蒸餾裝置中,經(jīng)過膜蒸餾處理(利用自身的疏水性,氣態(tài)分子可以透過蒸餾膜進(jìn)行轉(zhuǎn)移,液態(tài)分子則不能透過,即通過膜兩側(cè)組分的蒸氣壓差來達(dá)到蒸發(fā)的目的),形成水蒸氣和膜蒸餾濃縮液;S6、污泥的儲(chǔ)存:使S2中形成的污泥進(jìn)入污泥儲(chǔ)存裝置中并加以儲(chǔ)存,形成預(yù)處理污泥;S7、預(yù)處理污泥的固液分離:使S6中形成的預(yù)處理污泥進(jìn)入固液分離裝置中,經(jīng)過固液分離處理,形成固體組分和液體組分,并使所述液體組分重新進(jìn)入廢水收集裝置(1)中;S8、干化處理:使S5中形成的膜蒸餾濃縮液和S7中形成的固體組分進(jìn)入干化裝置中,利用熱源對(duì)所述蒸餾濃縮液和所述固體組分進(jìn)行干燥,形成水蒸氣和用于委外處置的固體廢棄物(包含從廢水中轉(zhuǎn)移來的非揮發(fā)性有機(jī)物和重金屬離子等成分);S9、水蒸氣的冷凝及回收:使S5和S8中形成的水蒸氣進(jìn)入冷凝裝置中,冷凝后與S3中形成的產(chǎn)水合并再利用(實(shí)現(xiàn)表面處理廢水的零排放處理)。在上述使用方法中,S1中所述混合利用攪拌或曝氣的方式來完成。在上述使用方法中,S2中所述破乳為氯化鈣(CaCl2)或氯化鈉(NaCl),所述混凝劑為聚合氯化鋁(PAC)(優(yōu)選質(zhì)量百分比濃度為5%~10%),所述絮凝劑為聚丙烯酰胺(PAM)(優(yōu)選質(zhì)量百分比濃度為0.1%~0.5%)。在上述使用方法中,S2中所述沉淀利用斜板沉淀池來完成,時(shí)間為2~4小時(shí)。在上述使用方法中,S3中所述精密過濾利用精密過濾器(優(yōu)選0.1~0.5μm)來完成,所述超濾利用超濾膜來完成,所述反滲透利用反滲透膜來完成。在上述使用方法中,S4中所述預(yù)熱的溫度為50~70℃。在上述使用方法中,S5中所述膜蒸餾利用疏水微孔膜來完成,膜外側(cè)為預(yù)熱濃水通路,膜內(nèi)側(cè)為空氣通路,控制膜外側(cè)蒸氣壓大于膜內(nèi)側(cè)蒸氣壓,壓差≤0.1MPa。在上述使用方法中,S7中所述固液分離利用板框壓濾機(jī)來完成。與現(xiàn)有技術(shù)相比,采用上述技術(shù)方案的本發(fā)明具有下列優(yōu)點(diǎn):1)本發(fā)明的處理系統(tǒng)及方法沒有借助化學(xué)氧化的手段,因而避免使用價(jià)格高昂的化學(xué)氧化藥劑,大大降低了生產(chǎn)成本;2)處理系統(tǒng)中的廢水收集裝置能夠混合調(diào)勻各路表面處理廢水,保證了水質(zhì)和水量的穩(wěn)定性,為廢水的可持續(xù)性處理奠定了基礎(chǔ);3)本發(fā)明的處理系統(tǒng)及方法能夠?qū)U水中的非揮發(fā)性有機(jī)物和重金屬離子等物質(zhì)轉(zhuǎn)移至固體廢棄物中,并通過委外處置的方式加以處理,避免了直接排放對(duì)環(huán)境造成的嚴(yán)重破壞;另外,處理過程中得到的產(chǎn)水能夠?qū)崿F(xiàn)回收再利用,避免了水資源的浪費(fèi),符合綠色環(huán)保的理念;4)與借助多級(jí)生物處理的系統(tǒng)相比,本發(fā)明的處理系統(tǒng)的占地面積大大減小,有利于大規(guī)模工業(yè)化推廣應(yīng)用。附圖說明圖1為本發(fā)明的表面處理廢水的處理系統(tǒng)及其使用方法的流程圖,其中附圖標(biāo)記的含義如下:1.廢水收集裝置;2.預(yù)處理裝置;3.膜處理裝置;4.預(yù)熱裝置;5.膜蒸餾裝置;6.污泥儲(chǔ)存裝置;7.固液分離裝置;8.干化裝置;9.冷凝裝置;S1.廢水的收集與混合;S2.混合廢水的預(yù)處理;S3.預(yù)處理上清液的膜處理;S4.濃水的預(yù)熱;S5.預(yù)熱濃水的膜蒸餾;S6.污泥的儲(chǔ)存;S7.預(yù)處理污泥的固液分離;S8.干化處理;S9.水蒸氣的冷凝及回收,虛線箭頭表示氣體行進(jìn)方向,實(shí)線箭頭表示液體行進(jìn)方向,虛實(shí)相間箭頭表示半固體或固體行進(jìn)方向。圖2為利用本發(fā)明的系統(tǒng)及其使用方法進(jìn)行表面處理廢水處理的流程圖。具體實(shí)施方式下面將結(jié)合附圖及具體實(shí)施例對(duì)本發(fā)明中的技術(shù)方案進(jìn)行詳細(xì)說明。如圖1所示,一種表面處理廢水的處理系統(tǒng)包括廢水收集裝置1、預(yù)處理裝置2、膜處理裝置3、預(yù)熱裝置4、膜蒸餾裝置5、污泥儲(chǔ)存裝置6、固液分離裝置7、干化裝置8和冷凝裝置9。廢水收集裝置1的出口通過控制閥與預(yù)處理裝置2的入口連通,用于使在廢水收集裝置1中混合的各路廢水進(jìn)入預(yù)處理裝置2。預(yù)處理裝置2具有兩個(gè)出口,其中一個(gè)出口(預(yù)處理上清液出口)通過控制閥與膜處理裝置3的入口連通,另一個(gè)出口(污泥出口)通過控制閥與污泥儲(chǔ)存裝置6的入口連通。膜處理裝置3具有兩個(gè)出口,其中一個(gè)出口(濃水出口)通過控制閥與預(yù)熱裝置4的入口連通,另一個(gè)出口(產(chǎn)水出口)通過控制閥將產(chǎn)水排出,以便進(jìn)行回收再利用。預(yù)熱裝置4的出口通過控制閥與膜蒸餾裝置5的入口連通。膜蒸餾裝置5具有兩個(gè)出口,其中一個(gè)出口(膜蒸餾濃縮液出口)通過控制閥與具有兩個(gè)入口的干化裝置8的其中一個(gè)入口(膜蒸餾濃縮液入口)連通,另一個(gè)出口(水蒸氣出口)通過控制閥與具有兩個(gè)入口的冷凝裝置9的其中一個(gè)入口連通。污泥儲(chǔ)存裝置6的出口通過控制閥與固液分離裝置7的入口連通。固液分離裝置7具有兩個(gè)出口,其中一個(gè)出口(固體組分出口)通過控制閥與具有兩個(gè)入口的干化裝置8的另一個(gè)入口(固體組分入口)連通,另一個(gè)出口(液體組分出口)通過控制閥與具有多個(gè)入口的廢水收集裝置1的其中一個(gè)入口連通。干化裝置8具有兩個(gè)出口,其中一個(gè)出口(水蒸氣出口)通過控制閥與具有兩個(gè)入口的冷凝裝置9的另一個(gè)入口連通,另一個(gè)出口(固廢出口)通過控制閥將固體廢棄物排出,以便進(jìn)行委外處置。上述表面處理廢水的處理系統(tǒng)的使用方法包括下列步驟:S1、廢水的收集與混合:將由脫脂、水洗、純水洗、硅烷處理等工段產(chǎn)生的各路廢水收集在廢水收集裝置1中,并利用攪拌機(jī)加以混合,形成混合廢水;S2、混合廢水的預(yù)處理:使S1中形成的混合廢水進(jìn)入預(yù)處理裝置2中,利用加藥泵加入氯化鈣,對(duì)表面處理廢水進(jìn)行破乳,破乳后調(diào)節(jié)廢水的pH值至8~10,利用加藥泵加入5wt%~10wt%的PAC和0.1wt%~0.5wt%的PAM,對(duì)表面處理廢水進(jìn)行混凝、絮凝處理,時(shí)間為0.2~1h,然后利用斜板沉淀池進(jìn)行沉淀,形成污泥和預(yù)處理上清液;S3、預(yù)處理上清液的膜處理:使S2中形成的預(yù)處理上清液進(jìn)入膜處理裝置3中,依次經(jīng)過0.1~0.5μm精密過濾器的精密過濾、超濾膜的超濾和反滲透膜的反滲透處理,形成產(chǎn)水和濃水;S4、濃水的預(yù)熱:使S3中形成的濃水進(jìn)入預(yù)熱裝置4中進(jìn)行50~70℃預(yù)熱,形成預(yù)熱濃水;S5、預(yù)熱濃水的膜蒸餾:使S4中形成的預(yù)熱濃水進(jìn)入膜蒸餾裝置5中,利用中空的疏水微孔膜進(jìn)行膜蒸餾處理,濃水通路為膜外側(cè),空氣通路為膜內(nèi)側(cè),并利用空壓機(jī)提供氣源;為了保證膜的質(zhì)量,要求膜外側(cè)壓力大于內(nèi)側(cè)壓力,壓力差≤0.1MPa,形成水蒸氣和膜蒸餾濃縮液;S6、污泥的儲(chǔ)存:利用污泥泵使S2中形成的污泥進(jìn)入污泥儲(chǔ)存裝置6中并加以儲(chǔ)存,形成預(yù)處理污泥,保證固液分離的滿負(fù)荷運(yùn)行;S7、預(yù)處理污泥的固液分離:使S6中形成的預(yù)處理污泥進(jìn)入固液分離裝置7中,利用板框壓濾機(jī)進(jìn)行固液分離處理,形成固體組分和液體組分,并使液體組分重新進(jìn)入廢水收集裝置1中;S8、干化處理:使S5中形成的膜蒸餾濃縮液和S7中形成的固體組分進(jìn)入干化裝置8中,利用余熱、廢熱源等對(duì)蒸餾濃縮液和固體組分進(jìn)行干燥,形成水蒸氣和固體廢棄物,固體廢棄物后續(xù)進(jìn)行委外處置;S9、水蒸氣的冷凝及回收:使S5和S8中形成的水蒸氣進(jìn)入冷凝裝置9中,冷凝后與S3中形成的產(chǎn)水合并再利用,實(shí)現(xiàn)表面處理廢水的零排放處理。具體實(shí)施案例:以江蘇某企業(yè)的表面處理廢水的處理過程為例來說明本發(fā)明中的系統(tǒng)及工藝方法的應(yīng)用,該企業(yè)生產(chǎn)不銹鋼掛具、鋁型材軌道、燈具配件等產(chǎn)品。該企業(yè)主要有脫脂、水洗、純水洗、硅烷轉(zhuǎn)化膜四個(gè)工段產(chǎn)生的廢水需要處理?;旌蠌U水總量為10.5m3/d,混合后的廢水水質(zhì)情況如下:pH值:7.5~9.5;電導(dǎo):6000~8000μs/cm;CODcr:2000~5000mg/L。由于該公司用水緊張,要求廢水全部回用,回用水質(zhì)要求如表1所示,但是常規(guī)的處理方法難以滿足企業(yè)要求。表1.企業(yè)表面處理廢水的回用水質(zhì)要求序號(hào)項(xiàng)目單位水質(zhì)控制指標(biāo)1pH—6.0~9.02電導(dǎo)率μs/cm≤5003懸浮物mg/L≤54濁度NTU≤35CODcrmg/L≤50因此,該企業(yè)利用本發(fā)明中的處理系統(tǒng)及方法進(jìn)行廢水處理,希望能夠?qū)崿F(xiàn)預(yù)期的效果,具體實(shí)施情況如下:使由脫脂、水洗、純水洗、硅烷處理四個(gè)工段產(chǎn)生的廢水流入廢水收集裝置,通過曝氣方式進(jìn)行混合調(diào)勻。利用廢水提升泵將廢水泵入預(yù)處理裝置,投加0.5%的氯化鈣進(jìn)行破乳,破乳后調(diào)節(jié)廢水pH值至8.5,然后按照1000ml/m3的用量,利用PAC加藥泵投加質(zhì)量百分比濃度為10%的PAC進(jìn)行混凝處理,再按照500ml/m3的用量,利用PAM加藥泵投加質(zhì)量百分比濃度為0.3%的PAM進(jìn)行絮凝處理,攪拌機(jī)攪拌20min,進(jìn)入斜板沉淀池進(jìn)行沉淀,沉淀時(shí)間為2.5h。將沉淀池上清液泵入膜處理系統(tǒng),膜處理包括0.1μm精密過濾器的精密過濾、超濾膜的超濾和RO膜的反滲透,RO處理的產(chǎn)水率為70%左右。使?jié)馑ㄟ^預(yù)熱器并加熱至50℃左右,然后進(jìn)入膜蒸餾裝置,蒸餾膜內(nèi)外側(cè)分別逆向流通RO濃水和空氣,空氣通路為膜內(nèi)側(cè),RO濃水通路為膜外側(cè),要求膜外側(cè)壓力大于內(nèi)側(cè)壓力,壓力差≤0.1MPa,91%左右的濃水轉(zhuǎn)化為水蒸汽,然后進(jìn)入冷凝器進(jìn)行冷卻,濃縮液產(chǎn)量僅為RO濃水的9%左右。利用板框壓濾機(jī)對(duì)污泥儲(chǔ)存裝置中的污泥進(jìn)行壓濾,壓濾產(chǎn)水回流至廢水收集裝置,壓濾污泥與膜蒸餾濃縮液混合,然后利用廠區(qū)廢熱進(jìn)行干化處理,水蒸汽進(jìn)入冷凝器進(jìn)行冷卻,冷卻水滿足表1中的回用水質(zhì)要求,干化污泥委外處置,最終實(shí)現(xiàn)了表面處理廢水零排放的目的,如圖2所示。RO處理產(chǎn)水與膜蒸餾冷凝產(chǎn)水進(jìn)行合并,所得產(chǎn)水的水質(zhì)情況如表2所示,通過對(duì)比可知,利用本發(fā)明的處理方法獲得的產(chǎn)水能夠滿足表1中的回用水質(zhì)要求。表2.利用本發(fā)明的處理方法獲得的產(chǎn)水的水質(zhì)情況以上所述,僅為本發(fā)明的一種具體實(shí)施方式,但本發(fā)明的保護(hù)范圍并不局限于此,任何熟悉本
技術(shù)領(lǐng)域:
的技術(shù)人員在本發(fā)明揭露的技術(shù)范圍內(nèi)可輕易想到的變化或替換都應(yīng)涵蓋在本發(fā)明的保護(hù)范圍之內(nèi)。因此,本發(fā)明的保護(hù)范圍應(yīng)該以權(quán)利要求書的保護(hù)范圍為準(zhǔn)。當(dāng)前第1頁1 2 3